tl;dr: Unexo, an over-the-counter drug manufacturer, recently faced scrutiny during an FDA inspection conducted from May 1, 2024, to May 14, 2024, led by inspectors Nicole Knowlton and Kellia Hicks. This inspection led to the Warning Letter by the USFDA ranging from inadequate documentation to improper facility maintenance. This article breaks down the key observations and their potential implications for Unexo’s operations and reputation.
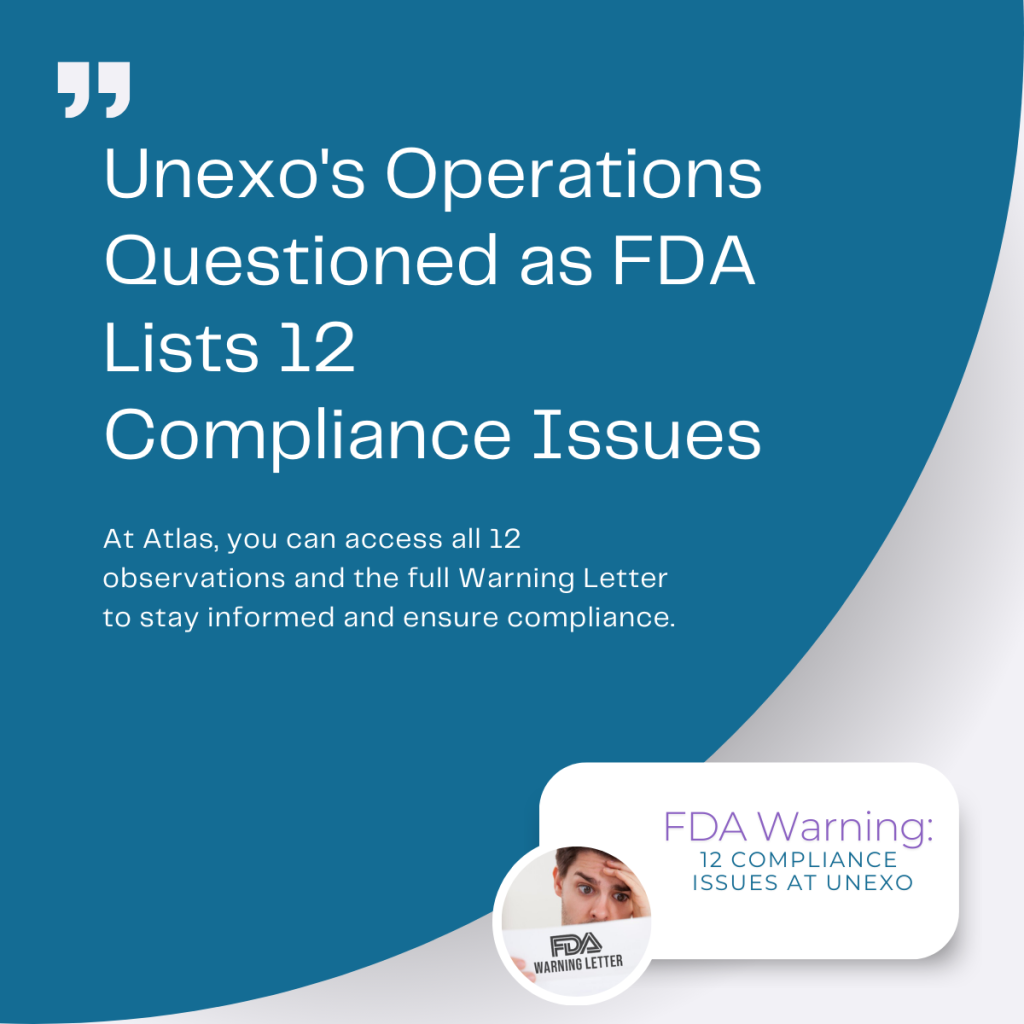
What were the 12 compliance issues identified during Unexo’s FDA inspection?
In a detailed review of Unexo’s facility, FDA inspectors identified serious shortcomings in regulatory compliance. The inspection, which lasted two weeks, culminated in a Form 483 report outlining 12 significant issues that raised questions about the company’s manufacturing standards and operational practices. These findings have drawn attention to potential risks associated with Unexo’s products and its commitment to quality.
Let’s take a closer look at the FDA’s observations:
1. Machine Usage Records Are Misleading
The Human-Machine Interface (HMI) indicated the last usage of key equipment was on April 21, 2024, marking the end of a production run. However, supporting batch records were missing, raising questions about its data integrity and record-keeping practices.
2. Inadequate Performance Qualification (PQ) Practices
- Unexo failed to produce a batch record supporting the performance qualification (PQ) of Machine P1, documented in its March 2022 report.
- Only two production runs were conducted during the PQ, lacking justification for this limited scope.
- Key operating parameters and equipment limits were not verified, undermining the credibility of their PQ process.
3. Facility Maintenance Issues
During a walkthrough on May 3, 2024, inspectors discovered a hole in the ceiling of the In-Process Quality Assurance (IPQA) area, exposing HVAC ducting. This poses risks to product quality and contaminates the manufacturing environment.
4. Uncontrolled Access to Labeling Materials
Inspectors noted unrestricted access to the storage area for labels and packaging materials. Labels in various stages of usage were found without proper lot numbers or quantity markings, a lapse that compromises traceability and control.
5. Lack of Detailed Written Procedures
Unexo lacked written procedures detailing the handling, storage, and testing of drug components, containers, and closures. Inspectors observed bins of finished products stored haphazardly, undermining product integrity.
6. Missing Lot Codes and Expiry Details
Numerous finished drug products in the production and storage areas lacked lot codes or expiration dates. Firm personnel were unable to identify the batches in question, a major lapse in traceability.
7. Inadequate In-Process Controls
The FDA found Unexo’s in-process validation protocols insufficient. Sampling schemes lacked statistical rigor, and key parameters during validation didn’t match those in production records.
8. Disorganized Batch Records
Inspectors found inconsistencies between the parameters listed in batch records and those in validation reports. For example, temperature and pressure settings used during validation were not reflected in production documentation.
9. Improper Documentation Practices
In the batch coding area, inspectors found assorted items, including incomplete cleaning records and packaging materials without lot codes or expiration dates. This reflects poor document management practices.
10. Lack of Verification for Equipment Limits
Unexo failed to update equipment specifications or verify critical manufacturing parameters. This oversight compromises the reproducibility and quality of their drug products.
11. Compromised Storage Practices
Inspectors observed bins of drug products stored without proper identification or status labeling. This lack of organization increases the risk of mix-ups and quality failures.
12. Deficient Process Validation Protocols
Unexo’s process validation reports lacked sufficient sampling and failed to ensure consistent manufacturing quality. These deficiencies cast doubt on their ability to produce compliant drug products.
What This Means for Unexo
The findings indicate systemic issues in its manufacturing processes, documentation practices, and facility maintenance. Non-compliance with FDA regulations not only jeopardizes product quality but also risks patient safety and brand reputation.
Addressing these observations requires a comprehensive overhaul of its quality systems. Immediate corrective and preventive actions (CAPAs) must focus on:
- Strengthening documentation and traceability.
- Conducting thorough validations with robust sampling.
- Ensuring facilities meet Good Manufacturing Practices (GMP).
- Training personnel to uphold regulatory standards.
Unexo’s response to this inspection will determine its ability to restore FDA confidence and maintain market credibility. Inadequate documentation and improper facility maintenance put the company’s operations and reputation at risk. However, Atlas can serve as a shield against such problems by providing in-depth insights into regulatory compliance. By analyzing millions of data points from global health agencies, Atlas helps companies like Unexo avoid similar pitfalls. With access to a comprehensive database of past FDA inspections, 483s, and investigator details, Atlas enables companies to learn from others’ mistakes, improve operational practices, and stay ahead of regulatory challenges. This proactive approach can help this company and others better prepare for inspections, reduce compliance risks, and safeguard their reputation.
With the issuance of a warning letter, it’s imperative for Unexo to meticulously review and strengthen its compliance measures. Each step towards addressing these issues is crucial to avoid further regulatory actions and prevent potential operational and reputational losses.
Stay tuned as we monitor Unexo’s next steps and their impact on the industry.