The Supplier Corrective Action Request (SCAR) process is crucial for product quality and supplier accountability in Quality Management Systems (QMS). It identifies and addresses nonconformance in products or processes to prevent recurrence, supporting continuous improvement.
This process is crucial in regulated industries such as pharmaceuticals, medical devices, and manufacturing, where the quality of materials impacts consumer safety. The FDA issued over 1,000 Warning Letters and close to 500 483s in recent years, highlighting the importance of having a well-defined SCAR process in place.
We understand that navigating the complexities of supplier nonconformance and regulatory scrutiny can be stressful, especially when a single oversight can impact product safety and compliance.
Now, let’s explore how the SCAR process begins with identifying nonconformance and notifying suppliers.
Identification and Initiation of SCAR
Identifying and initiating a SCAR is crucial for addressing supply chain nonconformances. This phase formally recognizes and communicates the issue to the supplier, paving the way for corrective actions. Proper initiation of the SCAR process ensures a swift resolution, prevents future occurrences, and maintains strong supplier relationships.
Let’s have a brief idea about it.
1. Identification of Nonconformance
Nonconformance occurs when a product or process does not meet established quality standards. It can be identified during various stages of production or after production.
Quickly identifying issues is essential to preventing further problems and ensuring that quality standards are met.
2. Formal Notification to Supplier
Once a nonconformance is identified, it’s important to formally notify the supplier using a SCAR document.
This document outlines the following:
- Description of the nonconformance.
- Product or batch affected.
- Expected corrective actions.
- Timeline for resolution.
Clear communication ensures the supplier understands the issue and the required steps to resolve it.
3. Details Included in the SCAR Document
The SCAR document should include the following:
- A clear description of the nonconformance.
- Affected product details.
- Corrective actions needed.
- A timeline for corrective action.
- Supporting evidence or documentation.
It ensures that the supplier can take appropriate action quickly.
Now that the initiation process is clear, let’s move to the next phase: the step-by-step SCAR process.
Step-by-Step SCAR Process
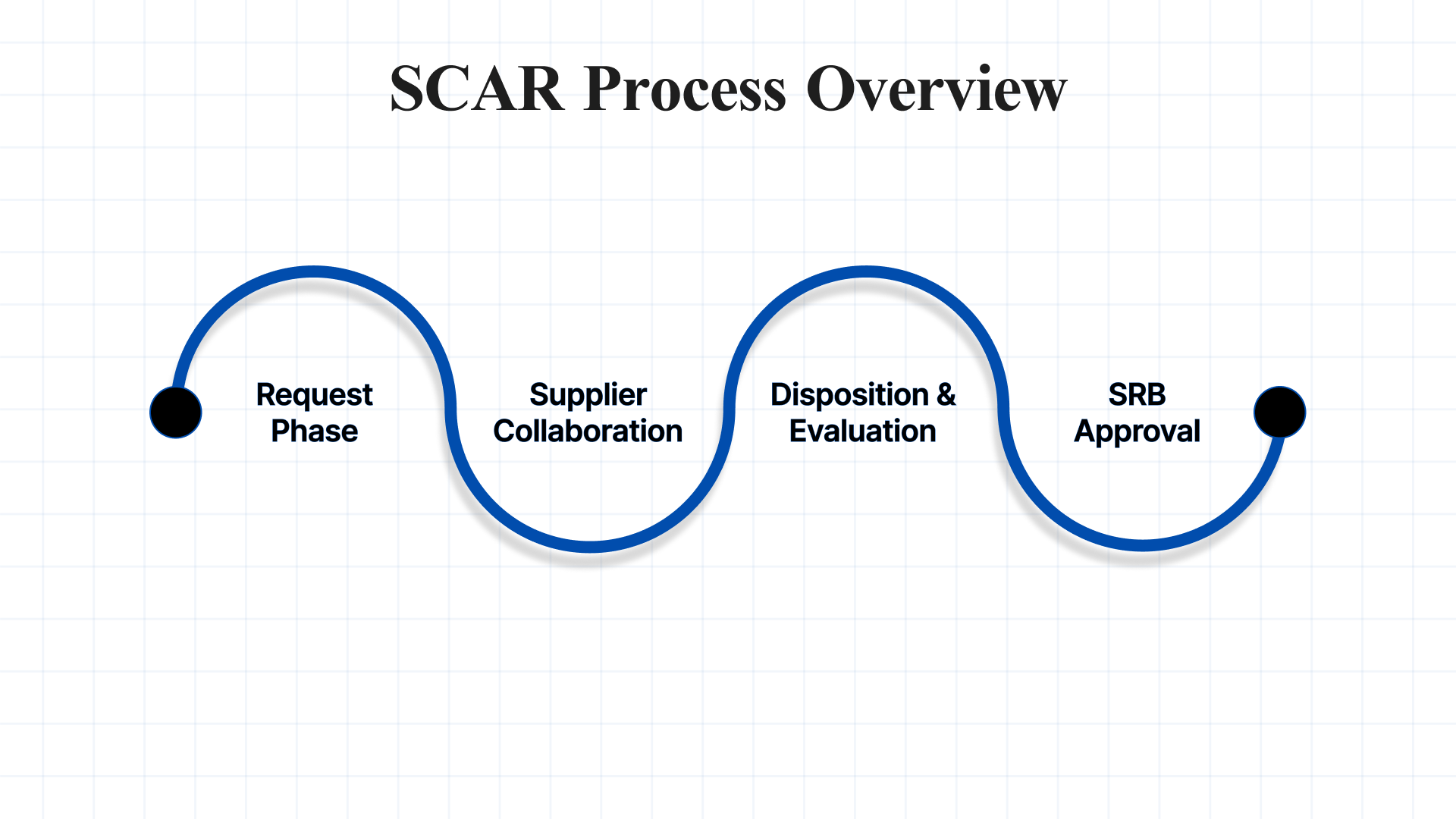
The SCAR process outlines actions taken after identifying a nonconformance with the supplier. This process ensures effective collaboration to resolve the issue, involving documentation gathering, supplier collaboration, response evaluation, and final approval from the Supplier Review Board (SRB) to close the matter.
Let’s discuss the Supplier Corrective Action Request (SCAR) process.
1. Request Phase
The SCAR process begins with the request phase, where the initiating organization provides the supplier with all necessary documentation related to the nonconformance.
The documentation includes the following:
- Product details and specifications.
- The nature of the nonconformance.
- Inspection or test results that support the issue.
- The expected corrective actions.
This documentation forms the basis for the supplier’s investigation and corrective action plan. Atlas-Compliance.ai aids this phase with AI tools for quickly searching historical FDA inspection reports and relevant documents to ensure all supporting documentation is accurate and complete.
2. Supplier Collaboration
Once the supplier receives the SCAR, collaboration begins. The supplier is expected to contain the issue, investigate the root cause, and analyze the factors contributing to the nonconformance. This phase includes:
- Containment: The supplier should implement temporary measures to prevent the nonconformance from affecting production or delivery.
- Investigation: The supplier must identify the root cause of the issue and assess the extent of the nonconformance.
- Analysis: A thorough analysis to determine why the issue occurred and how to prevent it from recurring.
It is necessary to perform predictive analytics and risk management evaluation to identify potential compliance issues early and prioritize corrective actions more effectively.
3. Disposition and Evaluation
Once the supplier has completed their investigation and proposed corrective actions, the organization evaluates the response.
This evaluation process includes the following:
- Reviewing the corrective actions suggested by the supplier.
- Assessing the feasibility of the proposed solutions.
- Determining if the actions address the root cause and prevent recurrence.
The evaluation ensures that the proposed solutions are effective and align with the organization’s quality standards.
4. Supplier Review Board (SRB) Approval
After the corrective actions have been evaluated, the Supplier Review Board (SRB) gives the final approval.
The Supplier Review Board (SRB) assesses the following details:
- The adequacy of the corrective actions.
- The timeline for implementation.
- Additional requirements for closure.
Once approved, the corrective actions are documented, and the SCAR is formally closed, ensuring that the issue is resolved.
Atlas-Compliance.ai can help streamline the documentation process, ensuring that all actions are well-recorded and compliant with regulatory standards, making the SRB approval process more efficient.
With the SCAR process established, the next step is to develop corrective and preventive actions (CAPA) to prevent recurrence. Let’s explore how this process works and the importance of root cause analysis for long-term solutions.
Developing Corrective and Preventive Actions (CAPA)
After completing the SCAR process, the next step is to develop Corrective and Preventive Actions (CAPA). This phase focuses on identifying the root cause of nonconformance and implementing actions to address the current issue and prevent recurrence.
- CAPA aims to enhance processes and products, ensuring consistent quality and regulatory compliance. Corrective actions tackle immediate issues, while preventive measures eliminate root causes of future problems.
- Corrective actions address current nonconformance, while preventive actions tackle the underlying process issues. By emphasizing both immediate and long-term solutions, organizations can reduce the risk of similar problems occurring again.
- A root cause analysis is essential to identify factors contributing to nonconformance. Without it, corrective actions may only address symptoms, leaving the problem unresolved.
This analysis pinpoints process weaknesses and supplier issues, enabling organizations to create a targeted action plan.
Steps to Develop CAPA
Developing an effective action plan involves several key steps:
- Define Corrective Actions: Clearly outline the steps needed to resolve the current nonconformance and prevent its recurrence.
- Assign Responsibilities: Identify who will be responsible for implementing each corrective and preventive action.
- Establish Timelines: Set realistic timelines for implementing the actions and achieving compliance.
- Allocate Resources: Ensure that the necessary resources, including personnel, tools, and materials, are available to implement the action plan effectively.
Once developed, the action plan should be documented and communicated clearly to all stakeholders to ensure alignment and accountability.
Atlas-Compliance.ai streamlines corrective and preventive action plans with tools for efficient documentation and tracking. Its database of past FDA inspections enables organizations to benchmark plans against industry standards and proposed outcomes, ensuring comprehensiveness in targeting the real issues before they occur.
With CAPA in place, it’s essential to ensure these actions are effective and compliant. Let’s explore how to follow up and verify CAPA implementation for long-term success.
Ensuring Effective Compliance
After implementing corrective and preventive actions (CAPA), the next crucial step is ensuring their effectiveness and compliance. This phase verifies that actions address current issues and prevent future occurrences while adhering to regulations.
Continuously monitoring and evaluating these actions is vital for maintaining product quality, regulatory compliance, and customer satisfaction.
Here is what you need to do to ensure effective compliance.
1. Follow-Up and Verification of Implementation
After corrective and preventive actions have been implemented, follow-up is necessary to confirm that they are being carried out as planned. Verification ensures that the actions have been fully executed and are working to address the root cause of the nonconformance.
This process includes the following steps:
- Conducting additional inspections or audits.
- Reviewing process performance data post-implementation
- Ensuring that the supplier has met all agreed-upon actions within the specified timeline.
Let’s have a look at methods that can help you evaluate the effectiveness.
Methods for Evaluating Solution Effectiveness
Evaluating the effectiveness of the implemented solutions is essential to ensure that the corrective and preventive actions have resolved the issue permanently.
Key methods for evaluating effectiveness include:
- Performance Metrics: Tracking specific performance indicators that reflect the success of the actions (e.g., defect rates, compliance audit results).
- Customer Feedback: Gathering feedback from internal teams or customers to ensure the solution is effectively addressing the problem.
- Re-testing or Re-inspection: Conducting additional tests or inspections to confirm that the product or process now meets the required standards.
Alignment with ISO Standards and Regulatory Compliance
Ensuring that corrective and preventive actions adhere to industry standards is crucial for maintaining regulatory compliance. Compliance with ISO standards and other regulatory requirements is essential for the pharmaceutical, medical device, and manufacturing sectors.
It guarantees that the actions taken not only address the immediate issue but also align with broader industry expectations and requirements.
Atlas-Compliance.ai supports regulatory compliance by offering access to current inspection reports, guidance on regulations, and tools for demonstrating adherence to ISO and FDA standards. Tracking compliance in the supply chain ensures that corrective actions align with regulations requirements.
Now, let’s explore how SCAR integrates with Quality Management Systems (QMS) for consistent documentation and improved compliance.
Integration with Quality Management Systems (QMS)
Integrating the SCAR process with a Quality Management System (QMS) is crucial for ensuring consistent documentation, traceability, and alignment with regulatory requirements.
An integrated SCAR process in a QMS enhances monitoring and management of supplier performance. Linking SCAR activities to quality processes ensures corrective actions are tracked and aligned with quality goals, improving efficiency and compliance in the supply chain.
Effective SCAR management needs proper documentation, which templates and digital tools in a QMS can facilitate. Templates streamline the SCAR process, ensuring all relevant details are standardized across suppliers and nonconformances.
Here is how you can simplify the process.
Benefits of Consistent Documentation within QMS
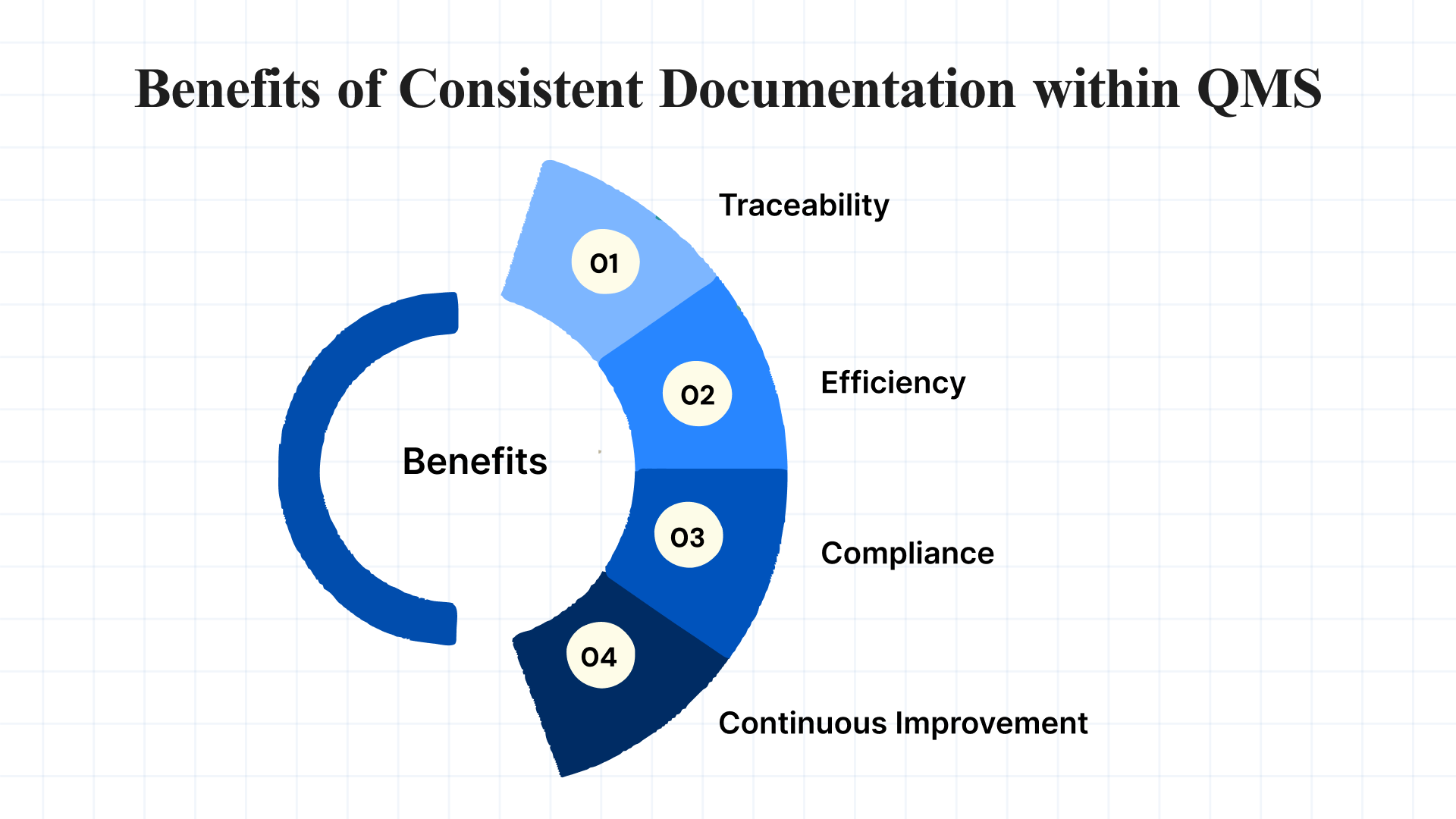
Having consistent and standardized documentation within a QMS offers several advantages, such as:
- Traceability: Clear records of SCARs and corrective actions taken, ensuring that the history of each nonconformance is accessible for future audits or inspections.
- Efficiency: Reduces manual paperwork, saving time and reducing the risk of human error.
- Compliance: Ensures that the SCAR process adheres to industry-specific standards and regulatory requirements, such as ISO 9001 and FDA regulations.
- Continuous Improvement: Consistent documentation allows for better analysis and identification of recurring issues, enabling the organization to take preventive actions.
Identify Cause and Effects Using eQMS
One of the key challenges in the SCAR process is demonstrating the relationship between nonconformance and corrective actions.
Using eQMS platforms can help you visualize the cause-and-effect relationship between root causes and corrective actions. This transparency is vital for audits, allowing organizations to demonstrate that actions were taken to address specific issues and prevent recurrence.
With Atlas-Compliance.ai, users can track and document each step of the SCAR process and link it directly to quality metrics and performance data within the QMS. This integration helps organizations create a comprehensive quality record, providing the evidence needed to demonstrate compliance with regulations and industry standards.
Now that we’ve explored how SCAR integrates with Quality Management Systems, let’s address nonconformance and implement strategies to prevent future SCARs.
How Atlas Compliance Can Help in the SCAR Process
Atlas-Compliance.ai is an AI-powered platform that optimizes every stage of the SCAR process, providing pharmaceutical companies with essential tools to manage nonconformance and ensure compliance.
From identifying nonconformances to tracking and verifying corrective actions, it streamlines and strengthens the entire SCAR process.
Here is how Atlas-Compliance.ai can assist you in the SCAR process:
- Predictive Analytics for Risk Identification: It uses machine learning and predictive analytics to analyze historical inspection data, helping organizations identify emerging risks and potential supplier nonconformances early. This proactive approach minimizes the likelihood of future SCARs.
- AI-Powered Document Search and Management: It integrates Natural Language Processing (NLP) to help organizations quickly search through large volumes of regulatory documents, such as FDA inspection reports. This AI-powered system improves data accuracy and efficiency in SCAR documentation.
- Comprehensive SCAR Documentation and Tracking: It provides a centralized platform to track SCARs from initiation to closure, ensuring all information—corrective actions, supplier communications, and approval statuses—are recorded and easily accessible, supporting audits and maintaining transparency.
- Regulatory Surveillance and Compliance Monitoring: The tool keeps organizations updated on FDA regulations and inspection outcomes, ensuring the SCAR process aligns with industry standards.
- Supplier Risk Management Tools: It helps assess and monitor supplier risks, ensuring all external partners meet regulatory requirements. Continuous performance tracking strengthens supplier relationships and prevents future nonconformances.
- Streamlining CAPA Development and Follow-Up: The tool simplifies the CAPA process by offering tools to document, track, and verify actions taken, while predictive analytics ensure that corrective actions are effective and comply with regulations.
With these capabilities, Atlas ensures an efficient, compliant, and proactive SCAR process. Let’s conclude our discussion and summarize the benefits of implementing SCAR effectively.
Conclusion
The SCAR process is essential for resolving nonconformances, enhancing supplier quality, and ensuring compliance. By promptly addressing issues and implementing preventive actions, organizations minimize risks and uphold high standards.
Atlas-Compliance.ai uses AI tools to streamline documentation, predict risks, and ensure ongoing compliance with industry regulations. With these tools, you can manage SCARs efficiently, strengthen supplier relationships, and stay ahead of compliance challenges.
Ready to optimize your SCAR process?
Discover how Atlas-Compliance.ai can help you stay inspection-ready and compliant.
Frequently Asked Questions
1. What is a Supplier Corrective Action Request (SCAR)?
A Supplier Corrective Action Request (SCAR) is a formal document issued by an organization to a supplier when a product or service fails to meet the required quality standards. It requests that the supplier investigate the issue, identify its root cause, and implement corrective actions to resolve the problem and prevent it from recurring.
2. When is it necessary to issue a SCAR to a supplier?
A SCAR should be issued when a supplier’s product or service fails to meet quality specifications, and informal attempts to resolve the issue have been unsuccessful. It is generally used for significant or recurring non-conformances that could impact the quality of the final product or regulatory compliance.
4. How is a SCAR different from a Corrective and Preventive Action (CAPA)?
While both SCAR and CAPA aim to address non-conformances, SCAR specifically focuses on supplier-related issues. CAPA encompasses a broader range of non-conformances, including internal processes, whereas SCAR is aimed at supplier problems, necessitating collaboration between the organization and the supplier to resolve and prevent future issues.
5. Why is root cause analysis important in the SCAR process?
Root cause analysis is crucial in the SCAR process because it helps identify the underlying factors that contributed to the non-conformance. By addressing the root cause, organizations can implement corrective actions that resolve the immediate issue and prevent similar problems from arising in the future.